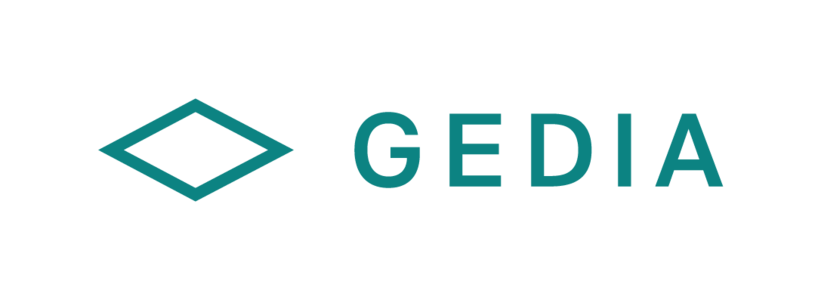
Operator/ Die Setter - Hot Forming (2nd Shift)
The job holder is responsible for setting dies and start the production process with respect to quality and economic efficiency.
Prepare Set-up and production:
Prepare tools for tool-change, check material availability and provide the necessary tools (i.e. conveyor, gauges, gripper, etc.). Complete the setup process with release of the production. If necessary, correct defects or faults or have them removed by specialist personnel (i.e. tool / machine maintenance). Initiate quality control by the Quality Assurance department and release the production process. Carry out necessary documentation.
Support the production process:
Support Press Operation (jumping function, changing the blanks, etc.) or, if necessary, taking over production activities.
Ensure that the machines, operating or auxiliary equipment are ready for operation: Periodically check the machines, operating devices or auxiliary equipment (e.g. feeding devices, conveyor, etc.) and carry out or initiate repairs if necessary.
Supporting the CIP:
Develop, suggest and implement possible technical and / or organizational optimizations after appropriate approvals by the supervisor.
Qualifications:
- Several years of experience in hotforming operations and die setting in the automotive supplier sector.
- Knowledge of progressive press set up processes, production processes and organization.
- Team player skills, persuasiveness, analytical mind and fast perception.
- Carry out the setup process and production preparation on the hotforming system and blanking line.
- Setup and operation of our new AP&T hot forming system.
- Training and instruction of hot form operators and monitoring of proper hotforming operation and quality specifications.
- Setting up, programming tools and releasing the production process with respect to quality, dates or deadlines, environment, health and safety regulations and economic efficiency.
- Active collaboration / Participation in setting up the production department and continuous improvement processes to develop, implement and improve technical and organizational structures.
- Ability and willingness to accept responsibility and to take the initiative in creating and utilizing opportunities of action and creativity.
- Ability to think innovatively, constructively and in a practical or an implementation-oriented manner.
- Identifying with the company, its functions and objectives.
- Ability to secure cooperation and expert support outside of one's own specialist/ organizational area of responsibility.
- Ability to work on group projects.
- Ability to proceed methodically and systematically to organize oneself and one's work.
- Ability to further develop oneself and the special field of work and duties and utilize this in the company.
- Ability to be always willing to learn – also in external special fields.
- Ability to deal responsibly with superiors and colleagues.
NO AGENCIES